Wire glass was widely utilized in buildings constructed in the late 1800s and early 1900s. At the time, it was considered to be the most innovative glazing product in terms of safety and aesthetics. Today, wire glass is often viewed as a historic feature to be conserved; however, there are several things to consider in regard to wire glass applications.
History
During the Industrial Revolution, the shift from skilled labor to large-scale manufacturing made the use of glass in building construction much more feasible. Plate glass was used in buildings where abundant light was needed, such as in factories, train stations, and greenhouses.
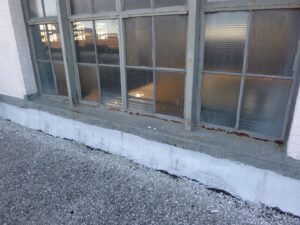
Issues arose with these glazing applications. The glass lites, which were installed in steel frames, shattered as a result of differential expansion and contraction between the respective materials. Additionally, many buildings were subject to intense vibrations, smoke, and heat from locomotives and machinery, which would result in broken glass. To address these safety hazards and maintenance issues, several options were explored, including using wire netting on the interior of the glass, wood framing instead of iron, and iron shutters. Each of these options presented advantages and disadvantages. The wire netting on the interior of the glass often corroded quickly from steam and also prevented workers from cleaning the glass. Furthermore, the openings in the netting were typically not small enough to capture all shards of glass when broken. The use of wood framing addressed the issues associated with expansion and contraction; however, the flammable nature of wood presented concern for industrial buildings such as factories and train stations. Lastly, the use of iron shutters protected worker from breaking glass, but they constantly required maintenance due to corrosion and ultimately blocked the much-needed light.
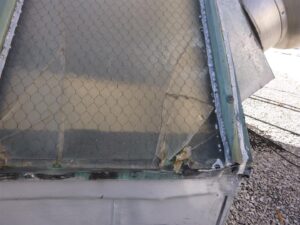
Following these failed solutions, a new product was born: wire glass. By embedding the metal wire netting within the glass, the issues regarding corrosion and maintenance were addressed. The wire glass also solved the issues related to expansion and contraction of its plate glass predecessor. At the turn of the 20th century, wire glass was advertised as shatterproof and fire retardant and quickly became widely utilized.
The decline of wire glass can be traced to the period of the World Wars. Due to wartime production needs, the availability of metal for wire glass diminished. Additionally, more economical and less complex types of glass, such as laminated, tempered, and float glass were developed.
Restoring or Replacing Historic Wire Glass: Things to Consider
Is your building historically significant?
If your building is listed on the National Register of Historic Places, it is important to maintain your existing wire glass features. Unfortunately, the types of wire glass that were utilized in the early 20th century are no longer produced today, There are salvage companies throughout the United States that can provide historic wire glass, although finding an exact match may prove to be difficult and large pieces are typically unavailable. While historic wire netting is not manufactured in the US, it may be obtained abroad, but lead times and cost may be prohibitive. It should be noted that there are currently no methods for repairing damaged historic wire glass. Once the glass has broken, the wire netting is exposed and is subject to corrosion. Epoxies or resins that could be used to fill cracks often discolor and are noticeable; therefore, replacement is the primary option for damaged wire glass.
Is maintaining the existing aesthetics important to you?
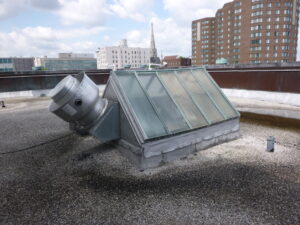
If maintaining the existing aesthetics is important, but perfect accuracy is not a concern, there are replacement wire glass products available in the United States. These products are typically thicker than historic wire glass and the wire netting often has a different patina. Additionally, the wire netting within this glass usually has a diamond pattern, whereas historic wire netting typically had a hexagonal or sinusoidal (“wavy”) pattern. As a result, the differences in thickness and aesthetics may require the replacement of more lites than anticipated.
If maintaining the existing aesthetics is not important and the project focus is to upgrade the glazing, glazing options are available to fit your current needs. There are numerous exterior glazing options beyond wire glass that can provide increased R-value, different levels of light emittance, patterns for privacy and light diffusion, etc.
Does your wire glass application meet building codes?
There are several applications where traditional wire glass is no longer acceptable. These include vision panels and sidelites. Safety wire glass, which incorporates a safety film for additional impact resistance, would be required to comply with building codes when installed at these locations. Building code research is recommended in advance of design and application to verify compliance.
Tagged In:
Building Enclosure Design & Consulting