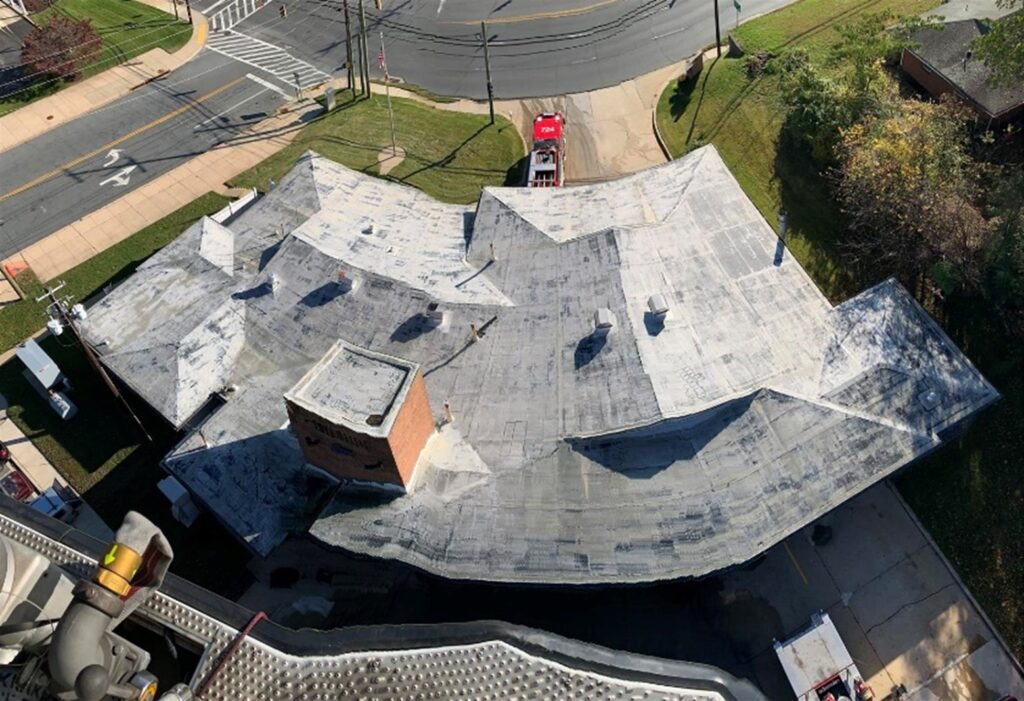
Firemen are used to harsh conditions. However, they do enjoy air conditioning from time to time. As part of systemic mechanical upgrades to several small fire stations, similar mechanical systems were retrofitted into the fire stations, which involved installation of mechanical equipment and piping into the attic or plenum space above the ceiling. At more than one fire station, shortly after the mechanical equipment was installed, occupants noticed stained/damp ceiling tiles. A check of the mechanical equipment indicated that everything was in order. Subsequently, the ceiling tiles were changed, and the matter was dismissed as an anomaly – until the next heat wave produced water dripping from the ceiling.
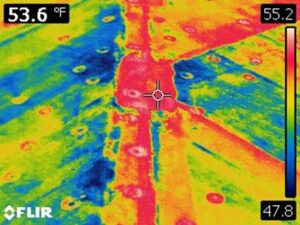
Evaluation of the existing conditions revealed that the attic was poorly insulated, and installation of the new mechanical equipment and piping had compromised the insulation by displacing what was there at many locations. The building had been designed with a 1-2” ft slope with roof level vents to provide ventilation of the interstitial space between the ceiling level and the plywood roof sheathing. Fiberglass insulation was placed at ceiling level.
The roof level vents allowed enough warm air interior the space that the new mechanical piping and equipment, under extreme loading, allowed the formation of condensation to the point where ceiling tiles became saturated. The infra-red image shows the hot air in the attic heating up the roof. Given the limited space in the attic, adding additional pipe insulation, or increasing the ceiling level insulation to envelope the piping was not feasible. The solution was to move the insulation entirely above the roof deck and close off the roof level vents.
Don’t let this happen to you! Although retrofitting mechanical equipment into attics is a common practice, consideration should be given to the existing insulation configuration and ventilation to minimize the chance of condensation.
Tagged In:
Building Enclosure Design & Consulting